ldpe plastic autoclave|autoclaving plastic parts : distributor Therefore, plastic ware may be sterilised but, if it needs to be de-pyrogenated, it is usually washed with pyrogen free water. . lab benches, autoclaves, lab ware, doorknobs, etc. are all frequently handled without gloves. All of these items, and virtually everything in a lab setting, are contaminated with these enzymes after contact with . La madera autoclave de Pino de Flandes se consigue con el tratamiento autoclave, también conocido como tratamiento de presión, aumentado su durabiliada y resistencia a la .
{plog:ftitle_list}
Discover the ultimate guide to steam (autoclave) sterilization for healthcare professionals. Learn the principles, processes, and critical role in patient care. In healthcare, ensuring the sterility of medical instruments is .
Low density polyethylene (LDPE), produced by free radical polymerization at a high reaction .A concise reference chart providing general compatibility guidelines for polymers and polymer . What Works and Doesn’t Work in an Autoclave. Let’s start by naming a few materials that are definite no-nos with autoclaving. Fortunately, it’s a short list: Polyethylene (PE) and its low- and high-density variants, LDPE .
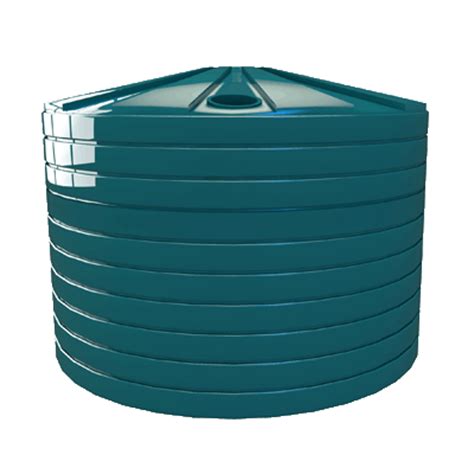
Polypropylene containers are autoclavable. The recommended autoclave cycle for empty containers is 121°C at 15 psi for 20 minutes. Care must be taken to allow free air circulation into and out of vessels during the autoclave cycle, .
Therefore, plastic ware may be sterilised but, if it needs to be de-pyrogenated, it is usually washed with pyrogen free water. . lab benches, autoclaves, lab ware, doorknobs, etc. are all frequently handled without gloves. All of these items, and virtually everything in a lab setting, are contaminated with these enzymes after contact with .Low density Polyethylene, LDPE, is a thermoplastic polymer made from the monomer ethylene.It is a highly branched plastic, which gives it a low density, as well as lower hardness, rigidity, and melting temperature.. LDPE was first produced in 1933 by Dr. John C. Swallow and M.W. Perrin of Imperial Chemical Industries (ICI) using a high-pressure process through free-radical .
Ethylene Oxide gas (EtO) is frequently used to sterilize materials that are otherwise too sensitive to heat or radiation sterilization. Many plastics fall into this category and EtO sterilization is frequently used for single use medical devices made of plastic. EtO gas requires careful handling because of its flammability and how poisonous it is.
The plastic made at Porvoo, Borealis, LDPE-Plant is low-density polyethylene (LDPE). The process has multiple steps on how the ethylene gas is polymerized using an autoclave reactor. These steps include raising the gas pressure in three steps, cooling the gas, gasHigh density polyethylene: LPDE: no: 80°C-100°C: Translucent: Low density polyethylene: Nylon: no : PFA: yes : Can be autoclaved repeatedly at 121°C/15PSI, 15 min. cycles: Polyacetal: yes : Can be sterilized by EtO, steam and autoclave, but degrades under high energy radiation. Polycarbonate (PC) yes: 135°C-135°C: TransparentHigh density polyethylene is used to make Nalgene bottles, carboys, . Autoclave: no. EtO: yes. Dry heat: no. Radiation: yes. Disinfectants: yes. Non-Cytotoxic [6]: Yes. . The ability of plastic materials to resist chemical attack and damage is dependent also on temperature, length of exposure to the chemical and added stresses such as .
Detailed models of industrial Low-density polyethylene (LDPE) autoclave reactors have been built by integrating several advanced modeling concepts: (a) An advanced thermodynamic model based on the Statistical Association Fluid Theory (SAFT) γ-Mie Equation of State, which represents molecules as chains of distinct functional groups [1-3]. .Dunkerque Plant (France) 240 – LDPE/EVA 2011 (Autoclave converted to tubular) Location Capacity (kt/y) 1st start up date Gela Plant (Italy) 70 - LDPE 1963 Ferrara Plant (Italy) 110 - LDPE 1976 Maracaibo Plant (Venezuela) 70 - LDPE 1976 Bratislava Plant (Slovakia) 90 – LDPE 1977 Dunkerque Plant (France) 190 - LDPE 1978 Umm Said Plant (Qatar . Low-density polyethylene (squeeze bottles, plastic bags, saran wrap) High-density polyethylene (shampoo bottles, bleach bottles, cutting boards) What are the Different Types of Autoclaves? There are two common types of autoclaves for steam sterilization: highspeed pre-vacuum autoclaves and gravity displacement autoclaves. Both types can be .
For example, you should not autoclave plastic bottles made from either Low Density Polyethylene (LDPE) or High Density Polyethylene (HDPE). These polymers have a narrow temperature range of between -50 and +80°C in the case of LDPE, and 100 to +120°C in the case of HDPE. . Before you autoclave plastic bottles it is advisable to use some .Polyethylene (PE) or high-density polyethylene (HDPE) Polystyrene (PS) Polyurethane or Polyurethane tubing; Polyvinyl Chloride (PVC) . Technically, you can autoclave everything on this list, but the plastic will either melt or weaken. Only autoclave these types of plastic when you need to dispose of them, and make sure you use biohazard bags . Most common plastic materials are polyethylene, polypropylene, polyvinyl chloride, polystyrene, polyethylene terephthalate etc., . radicals were not involved in the listed formulae. Onwudili et al. [22] also conducted high-pressure pyrolysis of polyethylene using an autoclave and reported a similar trend of product change with Kumari [31 .
The polyethylene we make may be classified into four major categories: Low Density Polyethylene - LDPE; High Density Polyethylene - HDPE; Linear Low Density Polyethylene - LLDPE; and Ethylene Vinyl Acetate Copolymers - EVA. . PAXOTHENE® LDPE resins are made by high pressure autoclave process and mainly used for blown film extrusion and .ECI Group offers proprietary autoclave and hybrid technology for high-pressure polyethylene. Our technology has been developed from the well-proven ICI autoclave process and is optimized to make use of modern materials, design .
Our lab sample bags are made from durable materials like LDPE (low-density polyethylene), providing strength and flexibility. These sterile plastic bags are designed to prevent contamination, ensuring your samples remain uncontaminated and reliable. . Improve the prep time, performance, microbial barrier and cleanliness of your autoclave peel .The first LDPE/EVA (Low Density Polyethylene / Ethylene Vinyl Acetate) autoclave process was introduced in 1938. In this type of application, a mix of pressurized ethylene gas and catalysts is stirred at high temperature in a vessel. The stirrer is turned by an electric motor which is in line with the vessel. Flexible: LDPE bends, stretches, and has low crystallinity. Moisture resistance: LDPE has no problem deflecting moisture and water. Impact and chemical resistance: LDPE won’t break down if it’s exposed to diluted or concentrated chemicals. Low price point: LDPE is fairly cheap to produce and can be recycled. Disadvantages:Both of these types of plastic are commonly used to make plastic containers and bins that are not rated as autoclave safe. The reasoning is simple. According to material selection platform SpecialChem , LDPE has a melting point between 105°C (221°F) and 115°C (239°F) and HDPE has a melting point between 120°C (248°F) and 140°C (284°F).
Currently, Low-Density Polyethylene (LDPE) manufacturing is predominantly carried out using two advanced methods—the stirred autoclave or the tubular route. Among these, the tubular processes are increasingly becoming the method of choice for many producers.Some of these tips are plastic, some are high density polyethylene. In general, pipette tips should only enter the autoclave as waste inside of an approved biohazards bag and always sterilized on a steam-producing setting. Book traversal links for Compatible/Incompatible Materials Lupotech Processes - LDPE and EVA. Lupotech is the market leader on high-pressure technology.Lupotech T, with its high conversion rates and effective heat recovery system, offers the lowest operating and investment costs.Lupotech A combines the strengths of Lupotech T with an autoclave vessel to provide EVA – copolymers with up to 40% VA content .
LDPE, LLDPE, & HDPE Polyethylene Comparisons LDPE LLDPE HDPE 20 Low Density Polyethylene •LDPE characterized by long chain branching. •Density range from 0.915 – 0.925 g/cc. •Autoclave grades generally offer excellent melt strength with minimal neck‐in combined with excellent drawdown in extrusion coating.For example, you should not autoclave plastic bottles made from either Low Density Polyethylene (LDPE) or High Density Polyethylene (HDPE). These polymers have a narrow temperature range of between -50 to +80°C in the case of LDPE, and while HDPE offers a wider range of between 100 to +120°C it is still below 121°C most commonly used for . To study runaway behavior in autoclave low-density polyethylene (LDPE) reactors, a kinetic model for a perfectly stirred tank reactor is presented. The kinetic model not only includes the standard initiation, propagation, and termination reactions for polymerization, but it also has free radical reactions that describe the decomposition of ethylene ultimately leading to a runaway.
POLYETHYLENE PRODUCTION TECHNOLOGIES PE Polymerization Techniques The route to PE falls into two categories: 1. High pressure polymerization • Produces LDPE • Operating pressure ranging from 1000 to 3000 barg • Operating temperature from 80 to 300 °C • Autoclave or tubular reactor • Free radical catalysts using initiators (peroxides)
qenos autoclave ldpe
ldpe for extrusion
ldpe extrusion coating
The whole process of water adding, temperature-rising, sterilizing, drying steam discharging controlled automatically. Steam-water inner circulation system: no steam discharge, and the .
ldpe plastic autoclave|autoclaving plastic parts